FAQ's
Enter keywords in the search box below:
EcoCuts, our services division, can cut your countertops to size, provide the sink cut outs, prepare seams, mitered waterfall edges, integral drainboards, etc – we can provide the edge details you specify and prefinish the tops and edges too. You’ll need to be able to supply dimensions for the parts you require, the sink, faucet, drop in stove brand and model number - plus the edge details etc that you want to see. Lead times are generally 6-8 weeks for custom made tops delivered.
To get a quote, please email drawings or dimensions to orders@ecosupplycenter.com when you have the sizes of the tops needed. You can also get a quote here.
Eventually, we’ll need the sink model number, as well as model numbers for the other fixtures mentioned above – but for an estimate, please tell us how many "sink cut outs" are required and we’ll input the general cost to mill that part – then list the other features you’ll need similarly & we’ll add the costs for those too. Backsplash will generally be made from the drop left over from the countertop millwork, so 4 – 5” height will generally be your max for good yield.
Let us know the address it’s delivering to – shipping the tops straight to your house is generally the most prudent because there will be fewer stops getting the tops into their installed location in your kitchen. But we can alternately ship the crated pallet to a commercial dock for a little less money if it seems feasible [or if your house is in a ravine or on a cliff, etc].
So- just provide these few bits of info with your dimensions & we’ll send your quote back itemized with materials, labor & freight broken out.
Associated Products:
To get samples of our products, simply fill out our sample request form.
If the samples you request are in-stock, generally they are packed and sent within 48 hours of your request, from our main office in Richmond, Virginia. Once the samples ship, you will receive an email with tracking information. (Please make sure to use a valid email to ensure you receive this information.)
Custom samples (i.e. larger samples, custom patterns, seamed samples, custom finishes, etc.) have a slightly longer lead time. Generally our fabrication division makes custom samples on Friday mornings, then they ship the following Monday once their finish is dry.
Shortly after your samples arrive, an EcoSupply representative from your area will contact you and accommodate any further questions or needs you may have.
Associated Products:
Yes, definitely. The first example below is Richlite used as bathroom partitions in the Museum of Chinese in America. You can also use Tekstur for partitions. The second example is from ZZQ, a restaurant in Richmond, Va.


BONUS: We can even pre-cut the partion walls for you! Please contact us for more information.
Associated Products:
Our team of skilled sales people are trained to look at your drawings, to understand your concepts and make recommendations based on the application and your project goals. We have a SKU system to ensure you list the correct Tekstur Panel on your product schedule.
Associated Product:
We do not recommend gluing Tekstur panels directly to the wall. Tekstur panels are generally classified as full thickness millwork panels and should be installed along the same guidelines as architectural grade plywood plywood and/or full thickness composite panels.
Associated Product:
Tekstur Panels can be installed with standard industry products and processes. Download our fabrication and install guide below. Please consult with ones of our expert sales people to recommend the best system for your project. Also, download our fabrication and install guide for comprehensive instructions.
Associated Product:
Our team of experts utilizes CAD/CAM design software and 3 axis milling techniques to engrave patterns into the surfaces of various materials. The arduous R&D process yields panel products that are balanced, efficient to process and manufactured to specification.
Associated Product:
Tekstur Panels can be fabricated with traditional woodworking tools and processes. The panels can be cut and machined to high tolerances without splitting or tear out. The surfaces need minimal treatment and in some applications may not need any additional applied finishes. Please download our fabrication and install guide for comprehensive instructions.
Associated Product:
Maintenance will vary depending on the chosen material and its application. Because of it’s durable attributes, the recycled paper-phenolic panels will typically need very little maintenance. If there is scuffing, in most cases, wiping the surface without a mild soap & water mixture will remove the scuff. If the panels somehow take on severe damage, you can order a duplicate replacement panel.
Associated Product:
We encourage design professionals to take advantage of our ability to turn their ideas into actual products. To receive a quote on a custom pattern, please send the following information to orders@ecosupplycenter.com, and one of our expert design consultants will contact you. You can also fill out our quote request form.
-DXF, DWG or Vector File of custom pattern
-Material Choice
-Depth of Cut
To fully realize your ideas, inquire to order a custom sample of your pattern on a specific material for a set up & processing Fee.
Associated Product:
The material can be finished for interior use in one of two ways: either sanded or unsanded – and afterward a finish is wiped on & off, for a non-reflective finish. All Richlite finishes are applied by your millworker or installer. If EcoSupply/EcoCuts is the fabricator on your project, we can apply your prefered finish.
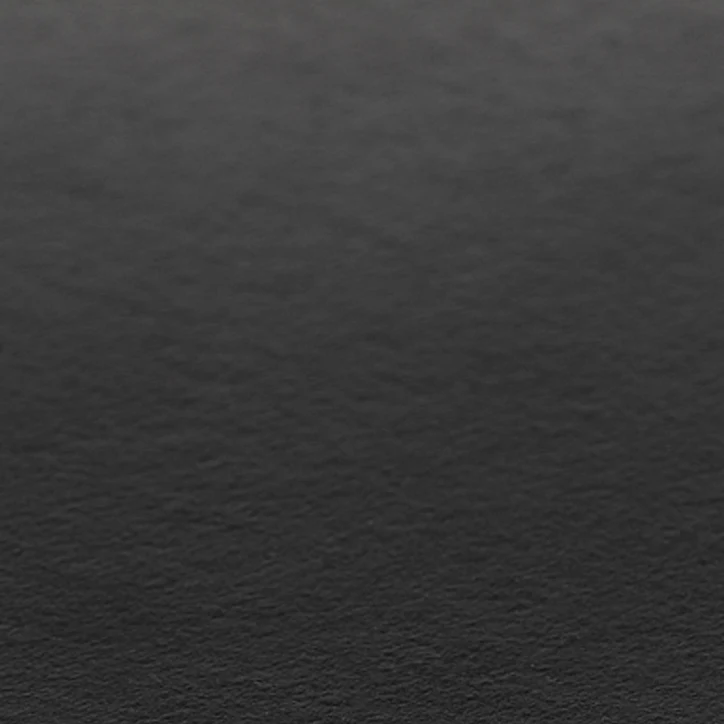
Richlite's "Leathered Finish" keeps the texture of Richlite, but an added applied finish enriches the color and adds a layer of protection. We prefer the unsanded version called "Leathered Finish" - because the shallow texture of the paper’s surface more successfully minimizes the first few scratches that will show up.
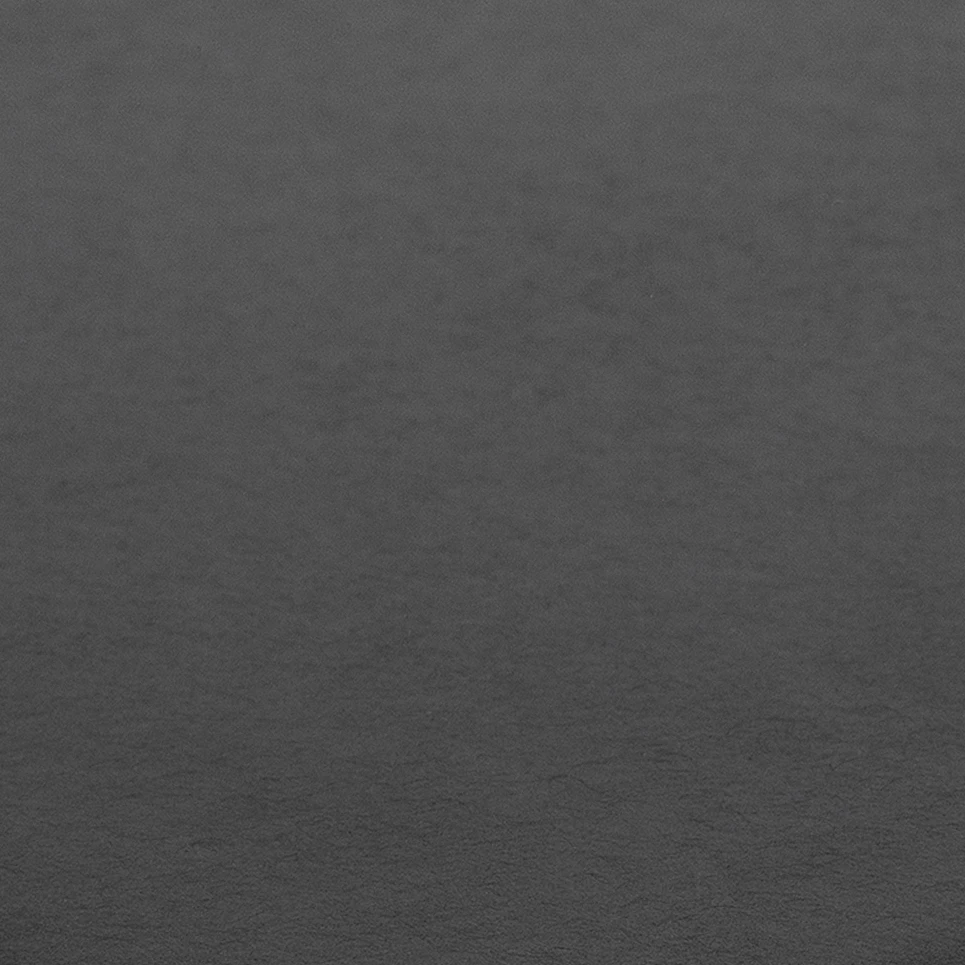
The "Honed Finish" requires a simple sanding process and an applied finish to achieve a honed, more satin, polished look than the "Leathered Finish". Scratches tend to be more apparent with this finish.
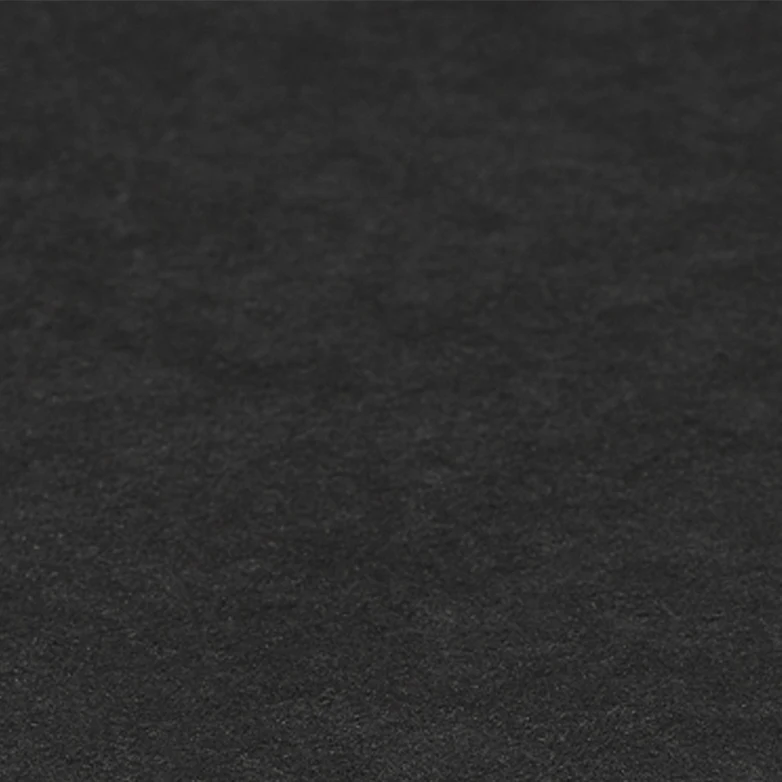
Richlite's "Mill Finish" is simply the surface of Richlite right out of the manufacturing process. This is the finish recommended for exterior use Best described as "no finish". Dust from shipping and/or storage can be removed with rain, water and a clean rag.
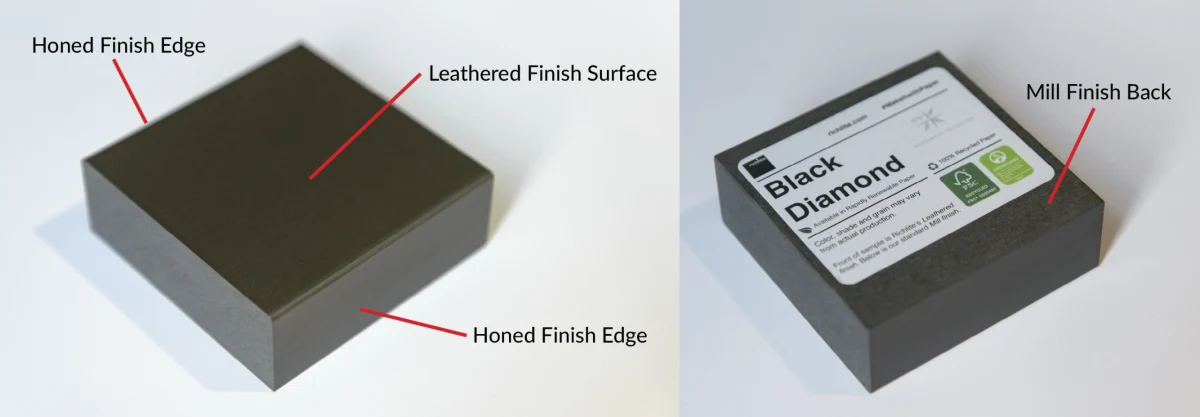
Standard stocked Richlite samples are 3" x 3" come with a leathered finish surface, 2 edges with a honed finish, and a mill finish back surface. Requests for samples with finishes different than the standard sample are considered custom samples and will have longer turnaround time. Here is what comes in the Richlite Architectural Sample Box.
Associated Product:
3/4" is the thinnest we recommend for an integral sink drainboard, and the thinnest that can be used for seams made with drawbolts milled into pockets on the underside of the countertop.
3/4" Richlite can be stacked to appear 1 1/2" thick and can cantilever 12" unsupported with no flex.
1" Richlite will cantilever 24" unsupported and will span 48" unsupported – noting that we could jump all over the top together while a micrometer reads no flex.
1" Richlite can be stacked to appear 2" thick.
3/4"-1 1/4" are the thicknesses that we can supply premade mitered waterfall edges that install with cam locks.
Associated Product:
Currently the Richlite Architectural Sample Box contains:
A Small Booklet featuring projects and products containing Richlite.
3" x 3" sample chips of the following:
- 1″ Black Diamond - Northwest Collection (Leathered Finish)
- 1/2″ Chocolate Glacier - Northwest Collection (Leathered Finish)
- 1/2″ Maple Valley - Northwest Collection (Leathered Finish)
- 1/2″ Browns Point - Northwest Collection (Leathered Finish)
- 1/2″ Redstone - Northwest Collection (Leathered Finish)
- 1/2" Rosedale - Northwest Collection (Mill Finish)
- 1/2″ Blue Canyon - Northwest Collection (Leathered Finish)
- 1/2″ Grays Harbor - Northwest Collection (Leathered Finish)
- 1/4″ Natural - Heritage Collection (Mill Finish)
- 1/4″ Slate - Heritage Collection (Mill Finish)
- 1/4″ r50 - Heritage Collection (Mill Finish)
- 1″ Stratum - Stratum Collection (Honed Finish)
- 1/2" Little Tahoma - Cascade Collection (Honed Finish)
- 1-1/4″ Rainier - Cascade Collection (Honed Finish)
- End Trim Example Piece
Click here to request a Richlite sample box
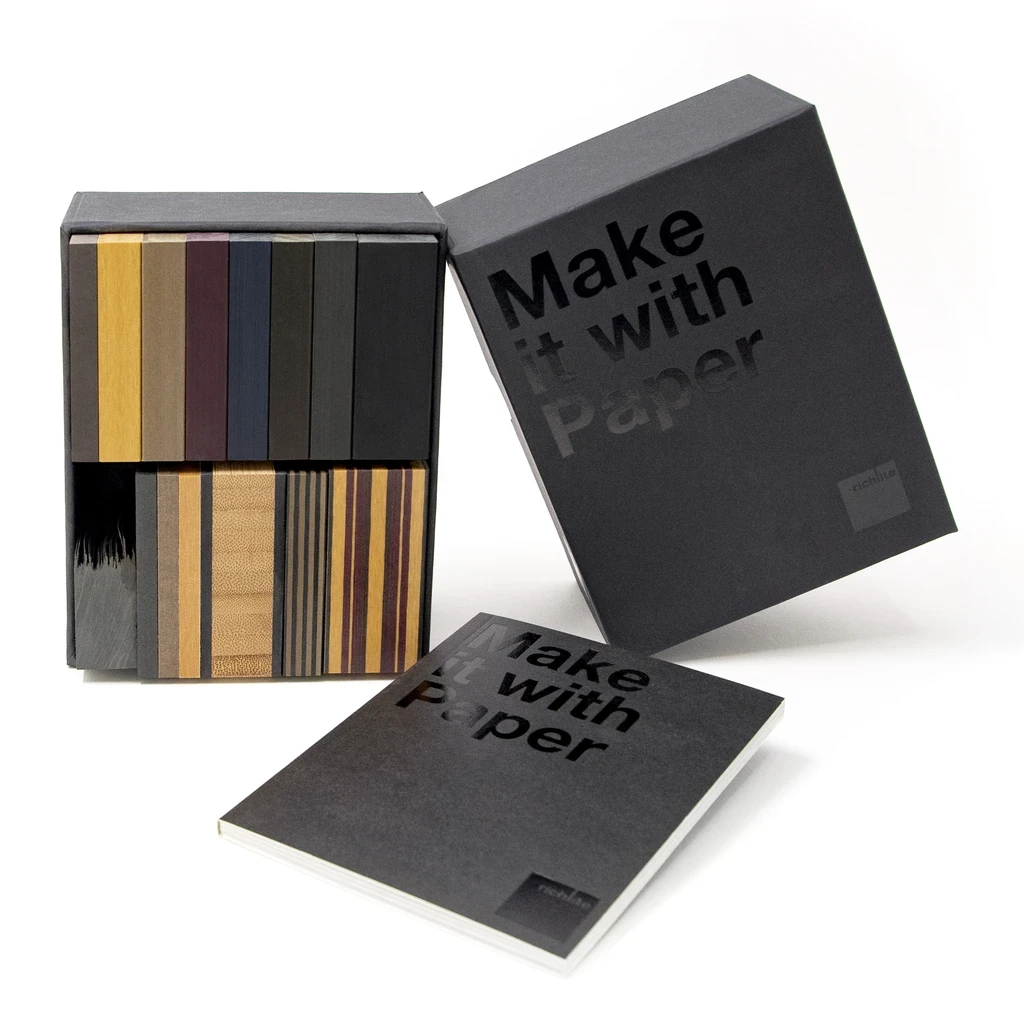
Standard Richlite samples come with a leathered finish surface, 2 edges with a honed finish, and a mill finish back surface.
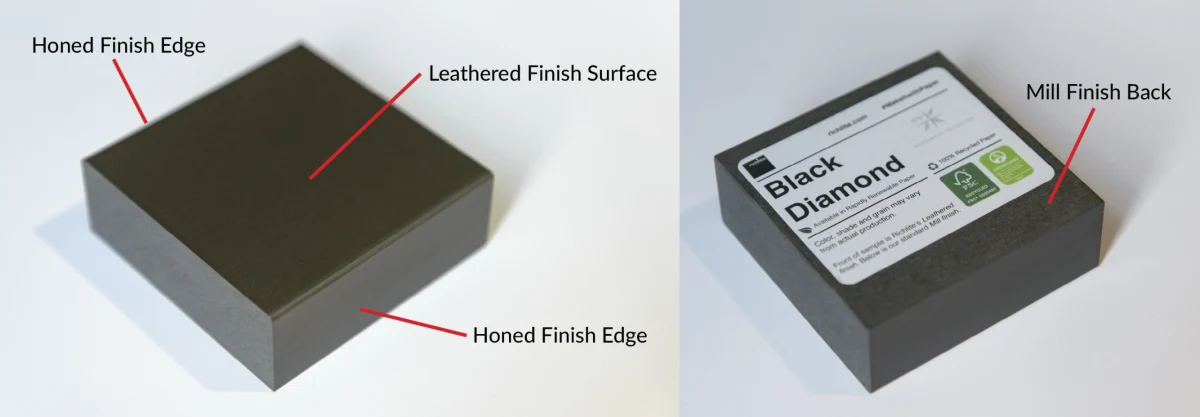
Requests for samples with finishes different than the standard sample are considered custom samples and will have longer turnaround time.
Associated Product:
We would make the comparison of Richlite to stainless steel restaurant work surfaces: both are strong, micro-clean and essentially inert; both will superficially mark but the Richlite will not scratch deeply except with real effort; both can be simply buffed out when cleaning to even out the surface; both will eventually develop an attractive living patina – in Richlite’s case, the finish isn’t going to prevent scuffing, but actually using the material will break it in and eventually create a soft, burnished soapstone appearance that resists scuffing as it ages. You can’t wear Richlite out, but you do wear it in.
If you or your clients are looking for a warm and natural, FSC certified, easy-to-work on, and impossible-to-destroy work surface...then Richlite is ideal for this application. If they are looking for an eternally picture-perfect surface then they might consider another material, perhaps one of the petro-based synthetics.
Richlite is, frankly, not for everyone… it has a very boutique attraction for those who wish to love what they live with and work on. And in addition to it’s practically bulletproof, anti-bacterial industrial performance standards, I think its warmth as well as its absurd durability are its greatest selling points.
Associated Product:
There is no written spec or step-by-step for casework using Richlite specifically – but please note the material is very strong and very heavy.
1/2” thickness is what EcoSupply would recommend using for the cabinetry, doors & drawer fronts.
Consider building the cabinet cases however your preferred shop is used to building them.
Please be aware: Richlite sheets are heavy, the cut edges are very sharp, you need pre-drill for any screws, and 24 hr cure structural epoxy is our preferred adhesive.
Richlite aces being glued to one another need to be sanded with 100 or 80 grit sandpaper before applying adhesive.
Shallow cup hinges are available for the thin doors. Regular 32mm hardware works fine with Richlite. Pre-drill or tap for hardware.
System 3 T-88 structural epoxy:
https://shop.ecosupplycenter.com/collections/finishes-adhesives/products/t-88-epoxy-u-tah-cartridge-tube
Consider using extra hinges for doors and soft close mechanisms for both doors & drawer fronts.
We have a nice bank of videos about machining Richlite here:
https://www.ecosupplycenter.com/professional-resources/videos/
See the full Richlite Fabrication Guide for more details attached below.
Associated Product:
Send it back to EcoSupply. Just contact us and we can help arrange shipment.
The manufacturer has a process which crushes cork insulation and facade panels back into granules. Generally, the granules are then used for the production of light concrete or as an infill for natural grass. Sometimes the granules are used as insulation again! Amorim Cork Insulation is 100% bio-based material and fully biodegradable. Because of the strength of the cork cells, it takes around 100 years to fully break down.
Associated Product:
Amorim Cork Insulation has a negative CO2 foot print: -596.50 kg/co2/m3. See the data in this PDF for more detailed information.
Having a negative CO2 footprint is unique. The cork is peeled from the oak tree with a very low energy process. The manufacturing process to turn the recycled waste from the cork wine industry into a building material is very low embodied energy, run on the cork granules, and uses no resin, binder, or any added material so product is 100% biobased material. Lastly the bark is harvested every 9 years and the tree will leave for 250+ years so the tree will sequester more CO2 in its lifespan than the entire manufacturing process of turning the bark into a building material, making Amorim Cork Insulation carbon negative.
Associated Product:
Custom samples (i.e. larger samples, custom patterns, seamed samples, custom finishes, etc.) have a slightly longer lead time. Generally our fabrication division makes custom samples on Friday mornings, then they ship the following Monday once their finish is dry.
To get samples of our products, simply fill out our sample request form.
Samples ship from our main office in Richmond, Virginia. Once the samples ship, you will receive an email with tracking information. (Please make sure to use a valid email to ensure you receive this information.)
Shortly after your samples arrive, an EcoSupply representative from your area will contact you and accommodate any further questions or needs you may have.
Associated Products:
We have put together a concise guide for helping you chose a panel thickness for Tekstur. See the attached document below:
Associated Product:
We have put together a guide on best practices for addressing different wall conditions and maintaining continuity in design. See the attached document below.
Associated Product:
Arbor Wood Co. produces Thermally Modified Wood for a variety of outdoor and indoor applications including siding, decking, and architectural millwork. Our process begins with a select grade of domestically grown and responsibly harvested timber which undergoes a thermal modification process using heat and steam. The result is a high-quality, performance-driven material that sustains the natural beauty and design element of wood all without the use of harsh chemicals.
High heat and steam replace chemicals to fundamentally modify Arbor Wood’s hemicellulose, making it one of the most natural, chemical-free ways to extend the service life of a wood product. The wood is less absorbent resulting in increased material stability with less warping/cupping and minimal expansion/contraction. Importantly, certain organic compounds are eliminated during modification thus removing the food source for rot and insects. The conversion of sugars to a nonfood source also turns the timber into a darker, richer through color, providing an appealing and refined aesthetic.
Arbor Wood Thermally Modified Wood is produced in a specialized, 3-phase kiln process using only heat and steam. In phase 1 an initial gradual increase in temperature reduces the equilibrium moisture content (EMC) of the wood. Phase 2 sees a rapid spike in temperature and is where the magic really happens. The cellular composition of the wood is altered in this high-heat, oxygen-deprived environment which breaks down the natural acids and sugars so as to no longer be a food source for mold, rot, or fungal decay. This change also renders the wood ‘hydrophobic’, meaning it loses much of the natural tendency to absorb water. As a natural byproduct of the process, Arbor Wood takes on a richer, darker tone throughout giving it a look similar to that of exotic species. The 3rd and final phase introduces steam to cool the wood down and bring the EMC back up to a suitable level. A benefit of this process is that Arbor Wood is dimensionally stable (meaning it won’t warp, rot, or chip), making it longer lasting and resistant to heat and weather, with an expected lifespan of 25+ years.
Associated Product:
Improved resistance to mold, rot and fungal decay as the naturally occurring food sources for these sorts of deterioration are converted or removed during the modification process. Arbor Wood is a natural wood product with the durability of an engineered material.
Improved dimensional stability, means that the wood is less susceptible to expansion and contraction due to temperature or humidity fluctuations. The process of thermal modification changes Arbor Wood’s relationship with water, thus creating a natural building material with the stability of an engineered product.
Lightweight and easy to work with! The reduced moisture content makes Arbor Wood lighter in weight than traditional wood building materials such as pressure-treated pine or even exotic hardwoods. As a result, many people find Arbor Wood easier to work with.
Associated Product:
Because our modification process can be applied to a range of wood species, there’s a good chance that options exist within most budgets. When compared to alternative options including composites, exotic hardwoods, and premium softwoods, Arbor Wood is competitively priced. And since we manufacture in the USA, our carbon footprint is lower than its exotic competitors.
Associated Product:
Thermal modification is a natural process using heat, steam, and a bit of pressure to significantly improve the durability and stability of many wood species. There are no harsh chemicals used during production and nothing nasty that can leach out over time. We support good forest stewardship to ensure that the wood we use is sourced domestically & sustainably to ensure a gentler footprint from start to finish.
Associated Product:
Arbor Wood Co. thermally modified wood can be used without additional finishes and expected to last 25+ years without any signs of serious physical degradation, warping or buckling.
However, a UV coating is recommended if color retention is an important factor to the client (we recommend CUTEK Extreme). If no UV coating is used, the wood will patina out to a natural silver.
CUTEK Extreme should be reapplied when the wood is no longer beading or as frequently as necessary to retain the natural or altered color of the wood. Timing will differ depending on many variables including the age and porosity of the wood, species, situation, design, aspect, weathered exposure and adequacy of preparation.
When considering frequency of maintenance there are two factors to consider:
Protection: CUTEK Extreme diffuses deeply into wood to provide long-term, cumulative, inside-out protection. Even when the wood surface has grayed and weathered, CUTEK Extreme will remain permanently mobile in the wood, meaning protection is not compromised even if the outward appearance of the wood has changed. Each additional coat of CUTEK Extreme provides further additional protection against moisture.
Appearance: To maintain the natural color of freshly oiled wood for longer or alter the appearance of your wood, CUTEK Extreme with an added CUTEK Colortone should be applied. Over time and with exposure to sunlight and UV, the color will slowly fade to a silver patina, or ware/erode with use. Color durability and the rate at which this fading, or wearing/eroding occurs is dependent on many factors, such as age and porosity of the wood, species, situation, design, aspect, and degree of exposure to the weather. CUTEK Extreme with an added Colortone should be reapplied as frequently as necessary to maintain desired color vibrancy.
Associated Product:
Have a Question?
Fill in your question and contact information below and we will send you an answer shortly.